Unlocking the Power of Screen Printing Silicone Ink
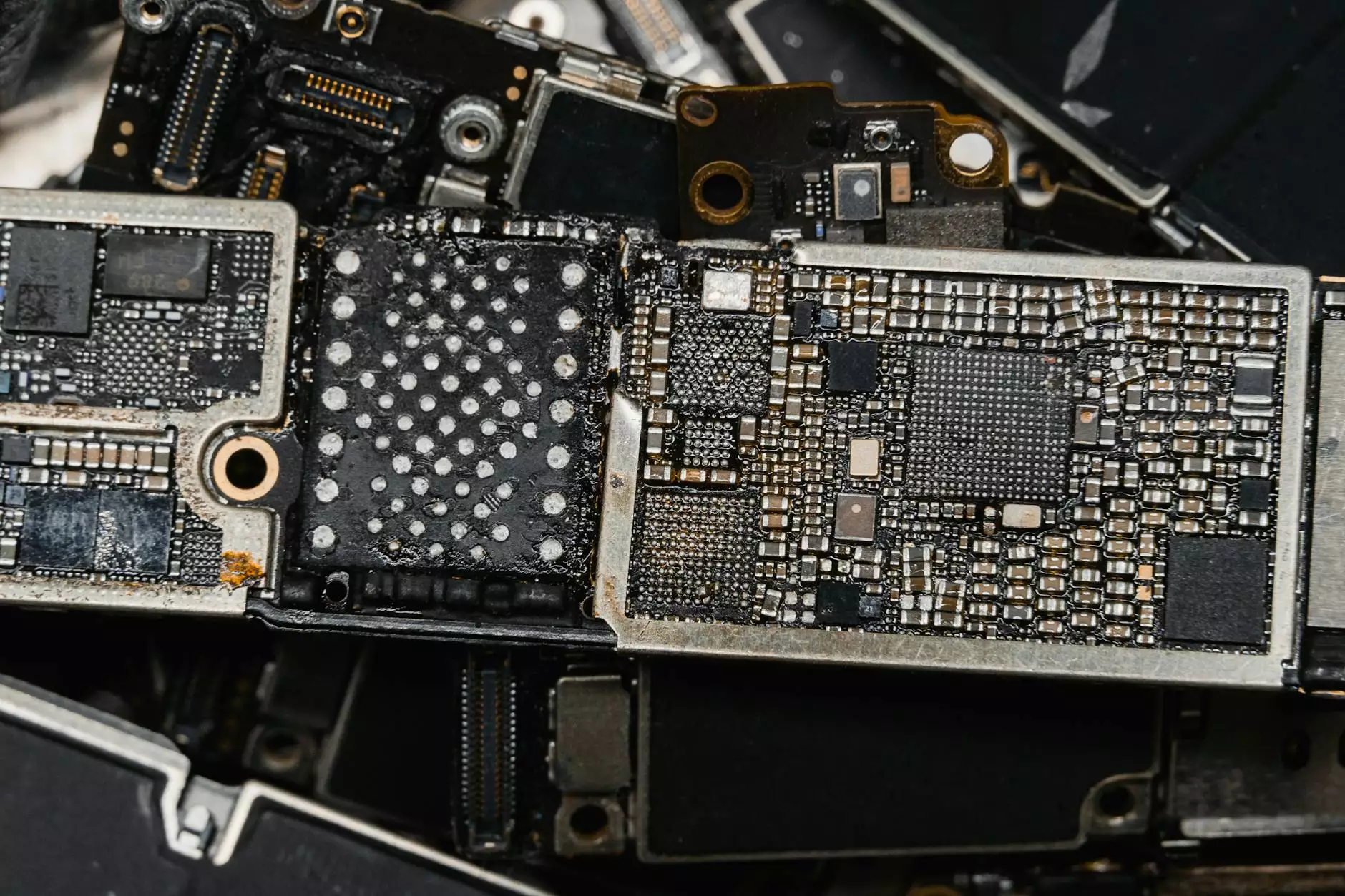
Introduction to Screen Printing Silicone Ink
When it comes to high-quality, durable, and vibrant printing, screen printing silicone ink emerges as a premier choice for businesses and artists alike. Unlike traditional inks, silicone-based inks offer flexibility, vibrancy, and durability, making them ideal for various applications, particularly in garment printing and product labeling.
What is Screen Printing Silicone Ink?
Screen printing silicone ink is a specialized ink formulated specifically for use in screen printing processes. This type of ink is primarily made from silicone resin, which provides unique properties when compared to standard water-based or plastisol inks. Here are some key characteristics:
- Flexibility: Silicone inks retain their flexibility even after curing, allowing printed designs to move seamlessly with the fabric.
- Durability: They exhibit excellent abrasion resistance and can withstand harsh conditions, making them perfect for outdoor applications.
- Vibrancy: Silicone ink can produce vibrant colors that maintain their brilliance over time without fading.
- Adhesion: They bond exceptionally well to a variety of substrates, including rubber, plastics, and fabrics.
Advantages of Using Silicone Ink in Screen Printing
Choosing screen printing silicone ink over traditional inks brings numerous advantages to your printing projects:
1. Enhanced Performance
Silicone inks are engineered to perform exceptionally well under various conditions. They maintain their integrity even when subjected to extreme temperatures and environmental conditions, making them a great choice for products that will see outdoor use.
2. Eco-Friendly Option
With a growing emphasis on sustainable practices, silicone inks stand out as a more eco-friendly option. They are less harmful to the environment compared to other inks that contain volatile organic compounds (VOCs).
3. Greater Design Versatility
With silicone ink, printers can achieve intricate designs and detailed graphics with ease. The ink is capable of creating fine lines and vivid effects, allowing for enhanced creativity in printing applications.
4. Superior Washability
Washing and wear can take a toll on printed materials. However, screen printing silicone ink is designed to resist fading and cracking, ensuring that your designs remain intact even after multiple washes.
Applications of Silicone Ink in Screen Printing
The versatility of screen printing silicone ink extends to various industries and applications:
- Apparel Printing: The textile industry has widely adopted silicone ink for printing on fabrics, especially those made from synthetic materials.
- Labeling and Packaging: Silicone ink is used extensively in creating durable labels that can withstand exposure to moisture and chemicals.
- Automotive Industry: Due to its durability, silicone ink is used in printing automotive products, including dashboards and components.
- Sports Equipment: From jerseys to sports gear, silicone inks provide flexibility and toughness needed for activewear.
Understanding the Screen Printing Process with Silicone Ink
The process of applying screen printing silicone ink involves several key stages:
1. Screen Preparation
The first step involves creating a stencil on a mesh screen. This stencil is produced using a light-sensitive emulsion that hardens when exposed to light. The parts that are not exposed will allow the silicone ink to pass through.
2. Mixing the Ink
Before printing, the silicone ink must be correctly mixed with the appropriate additives to ensure optimal viscosity and adherence to the substrate. This step is crucial for achieving the desired effects.
3. Printing
The screen is placed on the substrate, and a squeegee is used to push the silicone ink through the mesh. This process allows for precise control over ink application.
4. Curing
After printing, the ink needs to be cured to achieve durability. Curing involves heating the printed material to a specific temperature, allowing the silicone ink to bond effectively with the substrate.
Challenges and Considerations
While there are countless benefits to using screen printing silicone ink, it's essential to be aware of potential challenges:
1. Cost
Silicone inks can be more expensive than traditional inks due to their specialized formulation and superior quality. However, the long-term benefits often outweigh the immediate costs.
2. Technical Skill Required
Printing with silicone inks may require more technical skill to ensure the proper mixing and curing processes are followed. Training may be necessary to achieve desired results.
Why Choose Boston Industrial Solutions for Your Printing Needs?
At Boston Industrial Solutions, we understand the importance of high-quality printing solutions. Our expertise in screen printing silicone ink ensures that you receive the best service and results. Here’s why we stand out:
- Quality Assurance: We provide top-notch materials and inks that guarantee vibrant and long-lasting results.
- Experience: Our skilled team has years of experience in screen printing, ensuring proficient handling of every project.
- Customer Focused: We tailor our services to meet your specific printing requirements, delivering personalized solutions for each client.
- Innovative Techniques: Our commitment to adopting the latest technologies ensures efficient processes and superior product quality.
Conclusion
In conclusion, screen printing silicone ink is revolutionizing the printing industry with its unique properties and versatile applications. Whether you're looking to print apparel, labels, or any other products, silicone ink offers unmatched durability, flexibility, and vibrant colors that are bound to impress. By choosing Boston Industrial Solutions, you partner with an expert provider committed to excellence in every project.
Invest in your printing success with screen printing silicone ink and unlock a world of creative possibilities today!