The Booming Industry of Plastic Mold in China
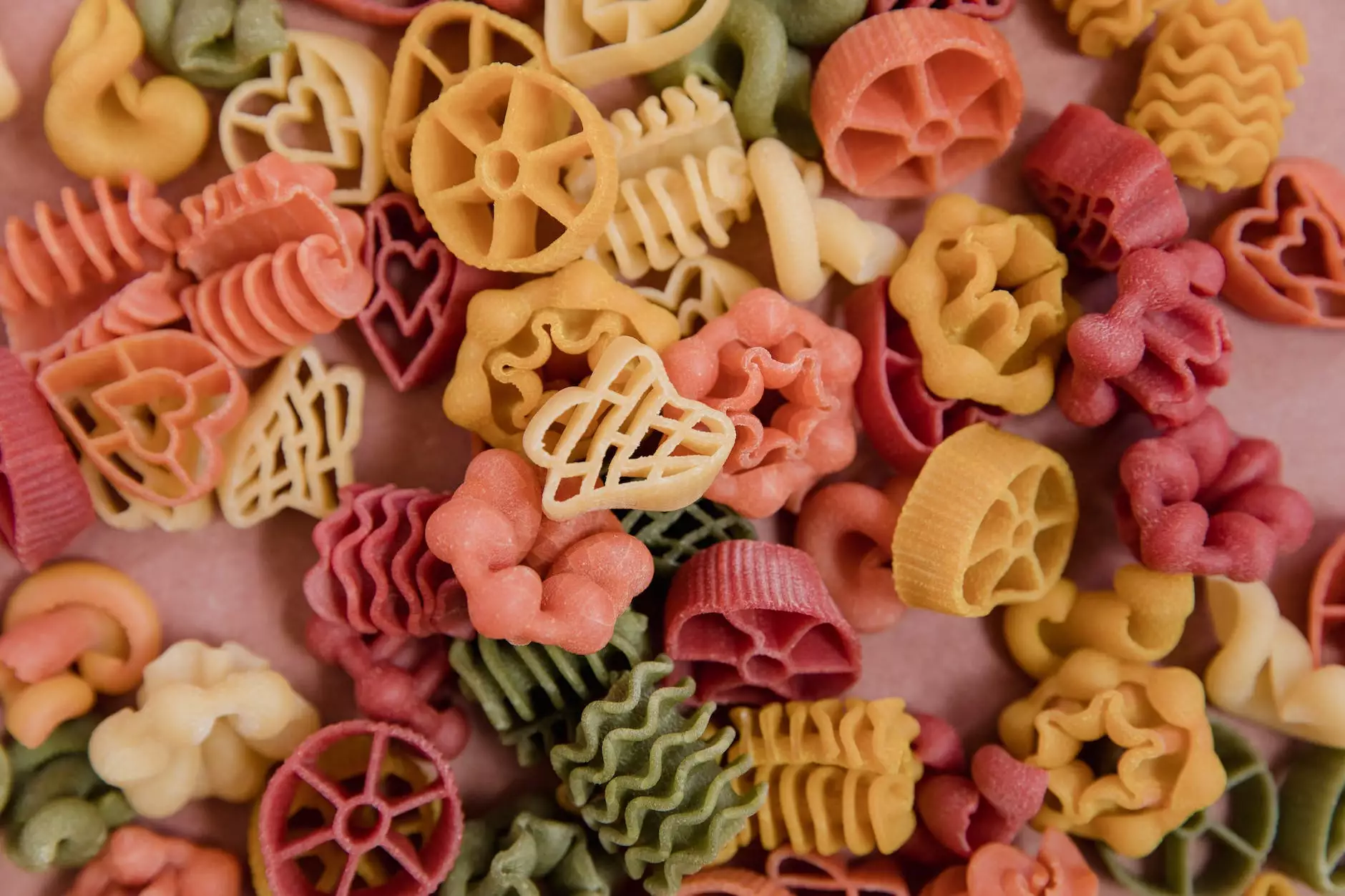
In recent years, China has emerged as a global leader in manufacturing, particularly in the realm of plastic mold production. This transformation can be attributed to the country's investment in advanced technologies, skilled labor, and a significant improvement in infrastructure. Companies like DeepMould.net, a renowned player in the field of metal fabricators, have been pivotal in this development, offering competitive solutions for both domestic and international clients.
What is Plastic Mold and Its Importance?
Plastic molds are essential tools used for shaping materials into desired forms. The process involves injecting molten plastic into a mold, where it cools and hardens into a specific shape. This method is integral to numerous industries, including automotive, consumer goods, medical devices, and electronics.
The importance of plastic molding lies in its ability to:
- Facilitate Mass Production: Plastic molds allow for the mass production of components with uniform consistency and precision.
- Reduce Waste: The process minimizes material wastage, making it environmentally friendly.
- Enhance Product Design: Advanced molding techniques enable intricate and innovative designs.
- Lower Manufacturing Costs: The efficiency of the process contributes to lower overall production costs.
China's Competitive Edge in Plastic Mold Manufacturing
China's dominance in the plastic mold industry is not accidental. Several factors contribute to its competitive edge:
1. Advanced Technology
Chinese manufacturers are increasingly adopting the latest technologies, including 3D printing, CNC machining, and automated systems. These advancements enable quicker production cycles and improved accuracy, which are crucial in maintaining quality while meeting market demands.
2. Skilled Workforce
The availability of a skilled workforce is paramount to the success of any industry. In China, a substantial number of engineering graduates enter the market each year, equipped with modern skills tailored to the needs of the manufacturing sector. This talent pool supports continuous innovation and improvement in the manufacturing processes.
3. Cost-Effective Solutions
One of the most compelling reasons businesses turn to plastic mold China is the cost-saving advantages. The lower labor costs, combined with high-volume production capabilities, allow manufacturers to offer incredibly competitive pricing without compromising quality.
4. Strong Supply Chain
China's extensive supply chain network enhances its capability to deliver materials promptly. Whether it is resin for injection molding or metals for fabricators like DeepMould.net, the proximity of suppliers and manufacturers fosters an efficient production environment.
The Role of DeepMould.net in the Plastic Mold Industry
As a significant player in the metal fabrication sector, DeepMould.net is at the forefront of adopting innovative practices in plastic molding. The company leverages state-of-the-art technologies and a commitment to quality to provide unmatched services.
Innovative Plastic Mold Solutions
DeepMould.net specializes in creating custom molds tailored to specific client requirements. Their cutting-edge technologies enable them to produce molds for various applications, ensuring that clients receive products that meet their exact specifications while adhering to tight deadlines.
Commitment to Quality
The dedication to quality is evident at every stage of the production process. DeepMould.net's rigorous testing and quality assurance measures ensure that every mold meets international standards, reducing the risk of production delays and operational inefficiencies for clients.
Sustainable Manufacturing Practices
In recognition of the importance of sustainability, DeepMould.net actively implements environmentally friendly practices. By minimizing waste through efficient production techniques and utilizing recyclable materials, the company not only reduces its carbon footprint but also positions itself as a responsible leader in the industry.
Future Trends in Plastic Mold Manufacturing
As the manufacturing landscape continues to evolve, several trends are set to shape the future of plastic molding in China:
1. Increased Automation
The trend towards automation is predicted to accelerate, with more manufacturers integrating robotics and AI technologies into the production process. This shift will enhance efficiency, reduce human error, and lower production costs even further.
2. Emphasis on Customization
As consumer preferences shift towards personalized products, the demand for customized plastic molds is expected to increase. Companies like DeepMould.net are well-positioned to adapt to these changes by offering flexible manufacturing solutions that cater to varying client needs.
3. Adoption of Smart Manufacturing Practices
The integration of digital technologies into manufacturing processes—often referred to as Industry 4.0—is on the rise. This includes the use of IoT (Internet of Things) for real-time monitoring and data collection, which can drive efficiency and innovation in *plastic mold production.
4. Global Expansion
As Chinese manufacturers continue to enhance their capabilities, a trend towards global expansion is likely. More and more companies will seek partnerships with Chinese manufacturers to leverage their expertise and competitive advantages in plastic mold production.
Conclusion
The future of plastic mold manufacturing in China looks incredibly promising. With the continuous advancement in technology, an abundance of skilled labor, and a focus on quality and sustainability, companies such as DeepMould.net are set to lead the charge in global manufacturing innovation. Businesses looking for efficient, cost-effective, and innovative solutions should consider the advantages offered by plastic mold China as a pathway to achieving their production goals.
By investing in partnerships with established manufacturers, companies can ensure they are at the forefront of the evolving landscape of plastic molding and innovation.