Understanding Vacuum System Components: A Comprehensive Guide
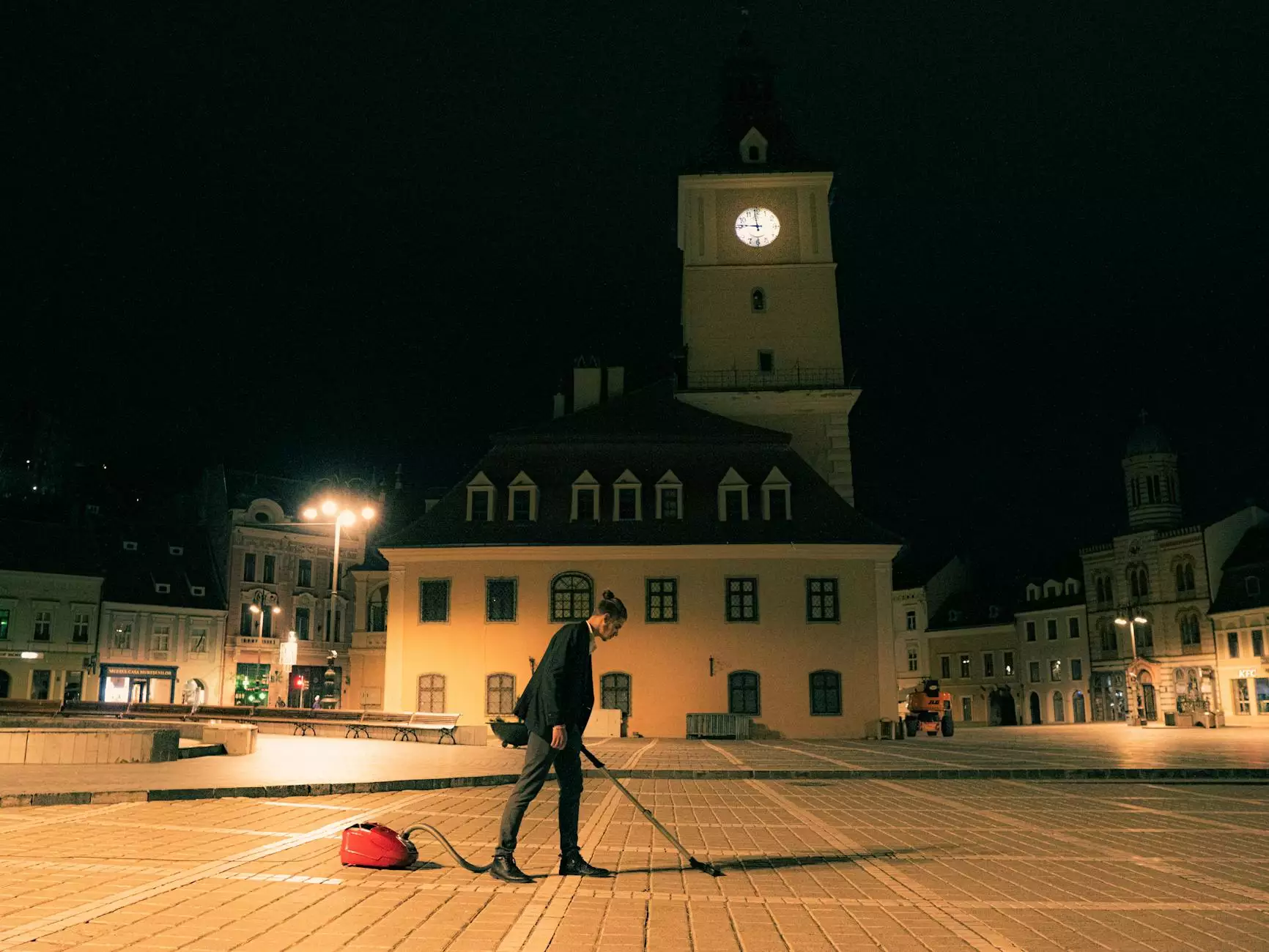
In today's fast-paced industrial landscape, the significance of vacuum system components cannot be overstated. These systems play a critical role in a variety of applications, from manufacturing to healthcare. This article aims to delve deep into the world of vacuum systems, detailing their components, functionality, and importance across different sectors.
The Basics of Vacuum Systems
A vacuum system essentially refers to a device that removes air and other gases from a sealed environment to create a vacuum. This process is vital for numerous applications, as it helps in:
- Reducing oxidation and contamination
- Enhancing product lifespan and quality
- Improving efficiency in production processes
Understanding the key components of these systems allows industries to optimize their operations and ensure consistent quality.
Key Components of Vacuum Systems
There are several critical components within a vacuum system that work in unison to maintain the desired vacuum level. Let’s explore each of these in detail:
1. Vacuum Pumps
Vacuum pumps are the heart of any vacuum system. They function by removing gas molecules from the desired space, creating a vacuum environment. Various types of vacuum pumps are available:
- Rotary Vane Pumps: Widely used due to their reliability, they're ideal for low to medium vacuum applications.
- Scroll Pumps: Known for their quiet operation and cleanliness, making them perfect for sensitive applications.
- Diaphragm Pumps: They use a flexible diaphragm to create a vacuum and are ideal for corrosive or dirty gases.
- Turbo Molecular Pumps: Used in high vacuum applications, these pumps are designed to handle extremely low pressures.
2. Vacuum Chambers
Vacuum chambers are sealed containers where the vacuum is created. They come in various shapes and sizes, depending on their intended application. Industries often customize these chambers to meet specific needs:
- Flat Chambers: Common in research, they are designed for easy access and sample observation.
- Spherical Chambers: These provide uniform thickness and pressure distribution, which is beneficial for high-stability applications.
- Custom Geometric Chambers: Businesses often design chambers according to their operational requirements.
3. Vacuum Gauges
Monitoring the vacuum level is crucial for maintaining operational efficiency. Vacuum gauges are instruments used to measure the pressure within the vacuum system. Types of gauges include:
- Capacitance Manometers: Offer precise measurements and can detect small changes in pressure.
- Piezoresistive Gauges: Commonly used in industrial applications for their reliability and accuracy.
- Thermocouple Gauges: Ideal for high vacuum applications, these gauges utilize temperature differences to measure pressure.
4. Valves
Valves play a pivotal role in controlling the flow of gases within the vacuum system. Their functionality can significantly affect operational efficiency. Here are some common types:
- Isolation Valves: Ensure no gas can enter or exit the vacuum system.
- Throttle Valves: Control the volume of gas that can enter the system.
- Relief Valves: Protect the system from over-pressure situations by releasing excess pressure when necessary.
5. Seal Systems
The effectiveness of a vacuum system often relies on its seals. Seal systems ensure that no gas enters or exits the vacuum chamber, thus maintaining the vacuum. Various seal types include:
- O-rings: Commonly used in applications for their versatility and ease of replacement.
- Gasket Seals: Ideal for static joints, providing high reliability.
- Metal Seals: Used in high-temperature applications, they offer outstanding performance but can be more complex to install.
6. Filters and Traps
Finally, filters and traps are essential components that protect vacuum pumps from contamination. They remove particulate matter and prevent corrosive gases from damaging the system. Types include:
- Particulate Filters: Capture dust and other solids that could obstruct the system.
- Oil Mist Filters: Essential for systems involving oil-sealed pumps to prevent oil contamination.
- Cold Traps: Used to condense and remove vapors before they reach the pump, protecting it from harmful substances.
Importance of Quality Vacuum System Components
The choice of high-quality vacuum system components is crucial for several reasons:
- Operational Efficiency: Quality components reduce energy consumption and enhance overall system performance.
- Longevity: Durable components are less prone to failure, ensuring a longer service life.
- Reduced Downtime: High-quality components minimize maintenance needs, reducing unexpected downtime.
- Enhanced Safety: Reliable vacuum systems reduce the risk of accidents related to pressure fluctuations.
Applications of Vacuum Systems
Vacuum systems have a wide range of applications across various industries. Here are some significant areas where they are crucial:
1. Manufacturing
In manufacturing, vacuum systems are used for:
- Material handling
- Thin-film deposition
- Packaging processes
2. Healthcare
The healthcare industry relies heavily on vacuum systems for:
- Medical suction devices
- Blood and fluid extraction
- Sterilization processes
3. Food Processing
In food processing, vacuum systems help with:
- Vacuum packaging
- Preservation of quality and freshness
- Extraction of flavors and aromas
4. Research and Development
Vacuum systems are essential tools in R&D for:
- Creating controlled environments
- Facilitating experiments requiring low pressures
- Testing materials under vacuum conditions
Choosing the Right Vacuum System Components
When selecting vacuum system components, businesses must consider several factors:
- Application Requirements: Understand the specific needs of your process to choose the right system.
- Performance Specs: Evaluate the pumping speed, ultimate pressure, and other performance characteristics.
- Compatibility: Ensure that all components work seamlessly together to avoid inefficiencies or failures.
- Manufacturer Reputation: Always choose components from reputable manufacturers known for quality and reliability.
Conclusion
In conclusion, vacuum system components are fundamental to various sectors and applications. Their ability to enhance efficiency, maintain product integrity, and ensure safety makes them indispensable in today's industries. By understanding the components and their significance, businesses can optimize their systems, ensuring higher operational standards and improved outcomes.
For more information about our advanced vacuum system solutions and to explore how they can benefit your business, visit tmm.com.tr.