The Transformative Power of Titanium Bolt Manufacturers
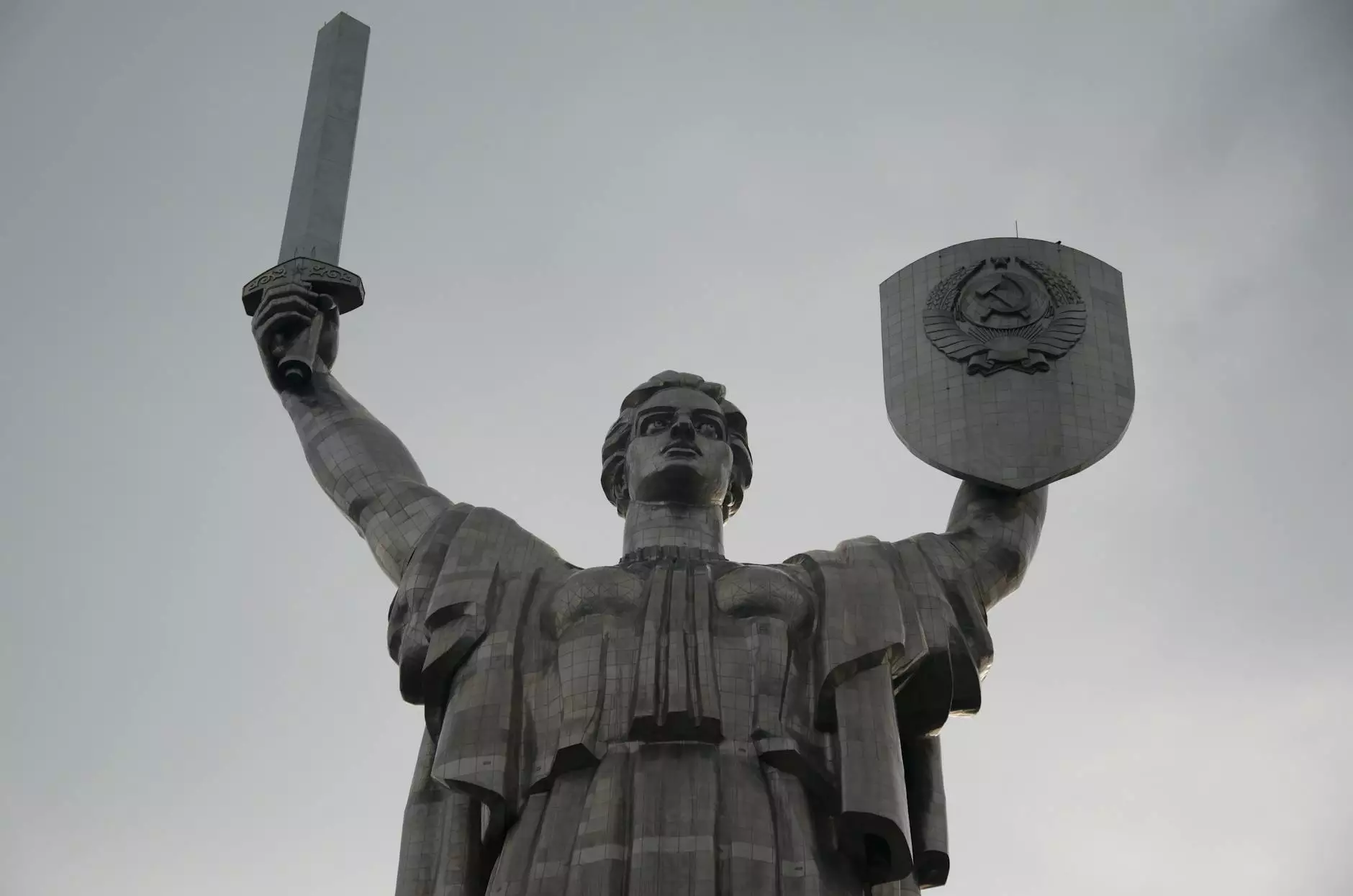
Titanium, recognized for its exceptional strength and corrosion resistance, has become a pivotal element in the manufacturing of bolts. As industries evolve, so does the demand for innovative materials that ensure durability and reliability. In this comprehensive guide, we delve into the world of titanium bolt manufacturers and explore their indispensable role for general contractors and engineers alike.
Understanding Titanium in Manufacturing
Titanium is a lightweight metal that boasts superior strength-to-weight ratio compared to traditional materials like steel. This quality makes it especially valuable in applications where performance and weight efficiency are critical. Below are some fundamental benefits of titanium:
- Corrosion Resistance: Titanium withstands harsh environments and does not rust, making it ideal for industries like marine, aerospace, and chemical processing.
- High Strength: It has a tensile strength comparable to that of some steels and is much stronger than aluminum, which contributes to its effectiveness in heavy-duty applications.
- Low Thermal Expansion: Titanium's expansion is minimal when exposed to varied temperatures, enhancing its reliability in high-heat environments.
- Biocompatibility: Titanium is non-toxic and is widely used in medical applications, particularly for implants and surgical tools.
The Role of Titanium Bolt Manufacturers
As the demand for titanium components increases, the role of titanium bolt manufacturers becomes more pronounced. These manufacturers are essential partners to general contractors, providing critical components for various construction projects. Here are several ways in which they contribute:
1. Supplying Quality Components
Quality is at the heart of every successful construction project. Titanium bolt manufacturers invest in advanced technology and quality control processes to ensure that each bolt meets strict performance standards. This focus on quality provides general contractors with confidence in the tools they are using, ultimately enhancing safety on job sites.
2. Customization Capabilities
No two projects are identical, and often, general contractors require specialized components designed to meet specific project needs. Many titanium bolt manufacturers offer custom manufacturing services, allowing for unique designs, sizes, and specifications that can accommodate any construction requirements.
3. Innovation in Design and Production
Today’s industrial challenges require innovative solutions. Manufacturers are continuously exploring new production methods and designs that improve efficiency and reduce material costs. These innovations are critical, especially as industries look to minimize waste and enhance sustainability.
4. Expertise and Support
The relationship between general contractors and titanium bolt manufacturers often extends beyond just a supplier dynamic. Manufacturers frequently provide invaluable support and expertise, assisting contractors in selecting the right products for their specific applications. This collaboration often translates into better project outcomes.
Applications of Titanium Bolts in Construction
Titanium bolts are increasingly used across various sectors in construction. Here are some primary applications:
Aerospace Engineering
The aerospace industry demands components that can withstand extreme conditions while remaining lightweight. Titanium bolts are a preferred choice due to their high strength and lightweight nature, which contribute to fuel efficiency in aircraft design.
Marine Applications
In marine environments, materials are subjected to saltwater conditions that expedite corrosion. Titanium's remarkable resistance makes it a favored option for fastening solutions in shipbuilding and offshore constructions.
Structural Engineering
Buildings and structures require fasteners that can endure substantial loads and stress over time. Titanium bolts offer the necessary strength and durability, ensuring the structural integrity of the overall architecture.
Automotive Industry
Modern automotive designs emphasize lightweight materials to improve fuel efficiency and performance. Titanium bolts are often used in high-performance vehicles where strength and weight savings are paramount.
Choosing the Right Titanium Bolt Manufacturer
Selecting the right manufacturer is crucial for general contractors. Here are some key factors to consider:
- Experience: Look for manufacturers that have a proven track record in the industry, showcasing experience in titanium bolt production.
- Certifications: Ensure that the manufacturer has the necessary certifications that attest to their compliance with industry standards, such as ISO 9001.
- Materials Used: Confirm that the manufacturer sources high-quality titanium alloys that meet the specific needs of your projects.
- Customer Testimonials: Seek out customer reviews or case studies that demonstrate the manufacturer’s reliability and service quality.
- Efficiency of Delivery: Timely delivery can significantly impact project schedules, so choose manufacturers known for their prompt service.
Environmental Considerations in Titanium Manufacturing
As sustainability becomes a more pressing concern, titanium bolt manufacturers are increasingly adopting eco-friendly practices. These practices may include:
Responsible Sourcing of Materials
Leading manufacturers ensure that the titanium used in their products is sourced responsibly, minimizing environmental impact and promoting ethical practices within the supply chain.
Energy-Efficient Production Processes
Investing in energy-efficient machinery and optimizing production processes can significantly reduce the carbon footprint associated with titanium bolt manufacturing.
Recycling Initiatives
Many manufacturers are now implementing recycling programs that allow for the reuse of titanium materials, thereby reducing waste and conserving resources.
Future Trends in Titanium Bolt Manufacturing
The future of titanium bolt manufacturers is poised for exciting developments. Here are some anticipated trends:
1. Advanced Manufacturing Technologies
The adoption of technologies such as 3D printing presents opportunities for producing complex and custom designs with reduced lead times.
2. Enhanced Material Properties
Research into new titanium alloys and treatments is expected to yield materials with enhanced performance features, expanding the potential applications for titanium bolts.
3. Integration of Smart Technologies
The incorporation of smart technologies, including sensors in fasteners, could lead to advancements in monitoring structural health and safety.
Conclusion
In conclusion, the role of titanium bolt manufacturers is vital in advancing the fields of construction and engineering. Their ability to deliver high-quality, durable, and innovative fastening solutions empowers general contractors to undertake complex projects with confidence. As industries continue embracing sustainability and technological innovation, titanium bolt manufacturers will undoubtedly remain at the forefront of these changes. By understanding the advantages and applications of titanium, stakeholders can make informed choices that lead to successful project outcomes.