Unleashing Innovation in Plastic Molding for Electrical Applications with DeepMould.net
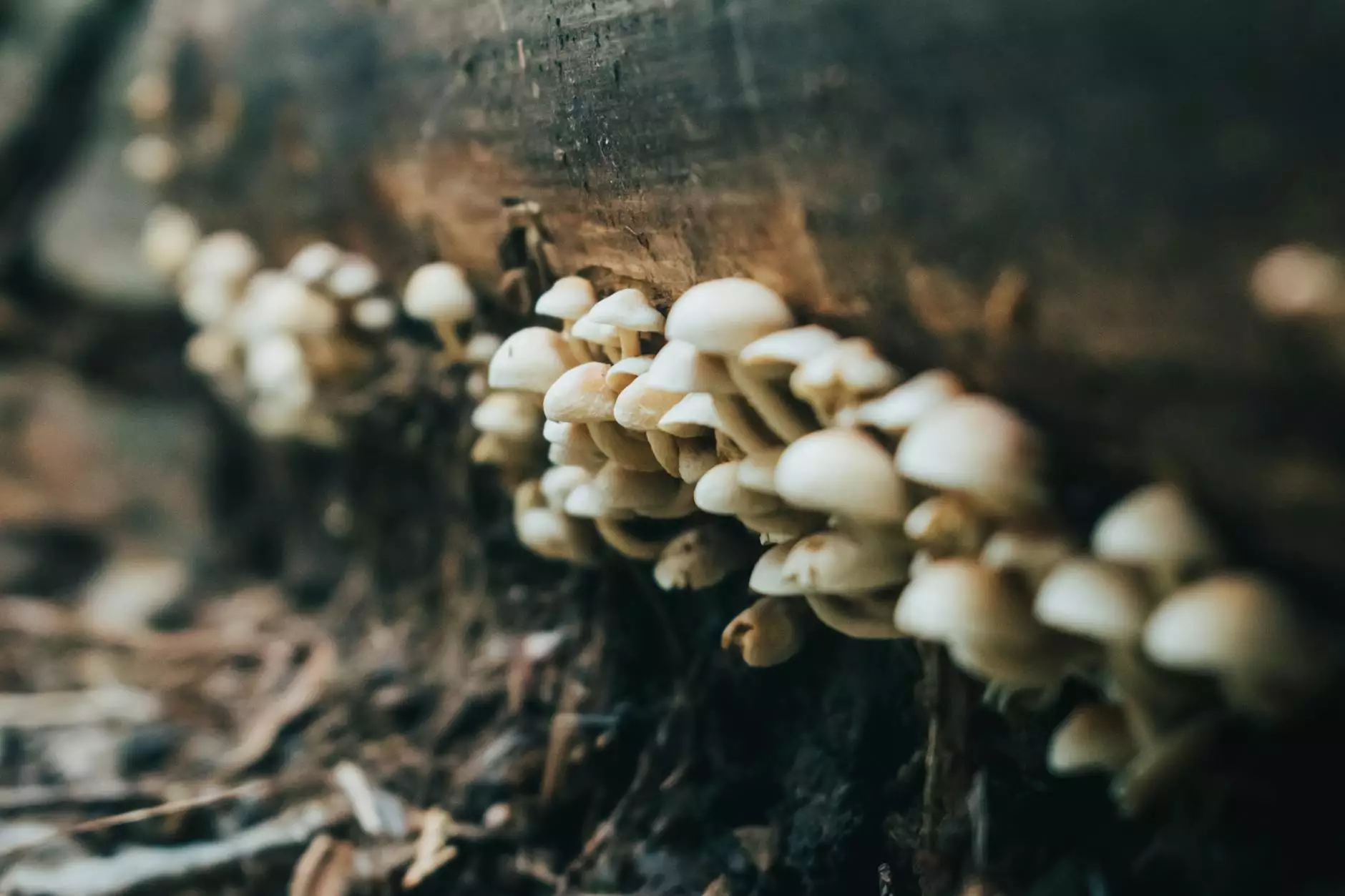
In the rapidly evolving electrical industry, the demand for reliable, durable, and precisely manufactured plastic components is higher than ever. As technology advances, electrical devices become more compact, efficient, and complex, requiring sophisticated manufacturing solutions. At DeepMould.net, we specialize in plastic molding for electrical, providing innovative, high-quality plastic solutions that meet the stringent needs of this dynamic industry.
Why Plastic Molding Is Crucial for Electrical Industry
Plastic molding serves as the backbone of modern electrical components and devices. Unlike traditional materials like metals or ceramics, plastics offer numerous advantages that are critical in electrical applications, including:
- Electrical Insulation: Plastics naturally resist electrical current, making them ideal for insulating electrical parts and preventing short circuits.
- Lightweight: Plastic components significantly reduce the overall weight of electrical devices, improving portability and ease of handling.
- Cost-Effective Manufacturing: Plastic molding processes such as injection molding allow for large-volume production at reduced costs.
- Design Flexibility: Plastics can be molded into complex shapes and intricate designs that would be difficult or impossible with metal or ceramic materials.
- Corrosion Resistance: Unlike metals, plastics are resistant to corrosion, ensuring longevity and reliability, especially in harsh environments.
The Role of DeepMould.net in Advancing Plastic Molding for Electrical Applications
DeepMould.net leads the industry with its comprehensive capabilities in plastic molding for electrical and a dedicated commitment to quality, innovation, and customer satisfaction. Our advanced manufacturing facilities, cutting-edge technology, and team of seasoned engineers enable us to deliver customized solutions tailored to the specific needs of electrical device manufacturers.
Types of Plastic Molding Processes for Electrical Components
At DeepMould.net, we employ a variety of plastic molding techniques optimized for electrical applications, including:
1. Injection Molding
The most prevalent method for producing electrical plastic components, injection molding allows for high-precision, fast-cycle production of complex parts such as connectors, housings, switches, and insulators.
2. Blow Molding
Used primarily for making hollow electrical parts like casings and tubes, blow molding ensures uniform wall thickness and high structural integrity.
3. Compression Molding
Ideal for large, bulky electrical components requiring excellent dimensional stability and heat resistance, compression molding produces durable parts from thermosetting plastics.
4. Thermoforming
Suitable for manufacturing electrical enclosures and covers with thin wall thicknesses, thermoforming offers speed and cost efficiency.
Materials Used in Plastic Molding for Electrical Applications
Choosing the right plastic material is crucial for the performance and safety of electrical components. DeepMould.net expertly works with a wide range of high-performance plastics, including:
- Polycarbonate (PC): Known for exceptional impact resistance and flame retardancy, ideal for rugged electrical housings.
- Polyamide (Nylon): Offers excellent mechanical strength, flexibility, and thermal stability.
- Polypropylene (PP): Used for insulating parts and connectors due to its chemical resistance and ease of molding.
- Polyester (PET and PBT): Provides excellent electrical insulation properties and dimensional stability.
- Modified Engineering Plastics: Such as PEEK and PSU, utilized in high-temperature or highly demanding electrical environments.
Designing for Success: Key Considerations in Plastic Molding for Electrical Components
Success in plastic molding for electrical hinges on meticulous design considerations. These include:
- Electrical Insulation Requirements: Ensuring the material and design prevent current leakage or shorts.
- Thermal Management: Designing components that can withstand heat generated during operation or environmental exposure.
- Mechanical Strength: Reinforcing critical areas to prevent failure under mechanical stress.
- Size and Tolerance: Achieving tight dimensional tolerances for proper fit and function.
- Ease of Assembly: Designing for manufacturability and efficient assembly processes.
Innovative Technologies Enhancing Plastic Molding for Electrical Industry
DeepMould.net stays at the forefront of technological advancements, integrating innovative tools like:
- Multi-Cavity Molds: For high-volume production with consistent quality.
- Rapid Prototyping: Using CNC machining and 3D printing to iterate designs quickly.
- Insert Molding: Combining metal and plastic components efficiently for enhanced electrical performance.
- Overmolding: Applying additional layers of plastic for insulation, sealing, or aesthetic appeal.
- Automation and Robotics: Ensuring precision and repeatability in production runs.
Quality Assurance and Testing in Plastic Molding for Electrical Devices
Reliability is paramount in electrical applications; hence, our quality assurance protocols are rigorous. These include:
- Material Testing: Ensuring compliance with industry standards for electrical, thermal, and mechanical properties.
- Mold Inspection and Maintenance: Regular checks to prevent defects that could compromise safety or performance.
- Dimensional Analysis: Using coordinate measuring machines (CMM) to verify tight tolerances.
- Electrical Testing: Confirming insulation resistance and dielectric strength.
- Environmental Testing: Assessing resistance to humidity, temperature extremes, and chemical exposure.
Customized Solutions for Diverse Electrical Industry Needs
DeepMould.net recognizes that the electrical sector encompasses a broad spectrum of components and applications. Our customized plastic molding solutions are tailored for:
- Consumer Electronics: Housings, switches, and connectors with sleek designs and high durability.
- Industrial Equipment: Ruggedized insulators, junction boxes, and control panels.
- Automotive Electrical Systems: Connectors, sensors, and housings engineered for high temperatures and vibration.
- Renewable Energy Systems: Plastic components resistant to environmental stressors, crucial in solar and wind energy devices.
- Medical Electrical Devices: Sterilizable, biocompatible, and highly precise components ensuring safety and reliability.
Advantages of Partnering with DeepMould.net for Plastic Molding in Electrical Applications
Collaborating with DeepMould.net translates into numerous benefits, including:
- Technical Expertise: Our team comprises seasoned engineers with extensive experience in electrical plastics.
- End-to-End Service: From design and prototyping to mass production and delivery.
- Rapid Turnaround: Using advanced machinery for shorter lead times.
- Competitive Pricing: Optimized processes that reduce costs without sacrificing quality.
- Sustainable Practices: Incorporating eco-friendly materials and manufacturing processes.
Driving Innovation and Efficiency in the Electrical Industry
As the world advances towards smarter, safer, and more efficient electrical systems, the importance of high-quality plastic molding for electrical components cannot be overstated. DeepMould.net is dedicated to fostering innovation, streamlining manufacturing, and ensuring the highest standards of quality to give our clients a competitive edge.
Conclusion
Whether you require complex plastic housings, insulators, connectors, or custom electrical components, DeepMould.net offers unmatched expertise and technology in plastic molding for electrical. Our commitment to excellence, detailed attention to design, and comprehensive quality assurance make us your ideal partner for all molded plastic solutions in the electrical industry.
Embrace the future of electrical manufacturing with confidence — choose DeepMould.net for innovative, reliable, and cost-effective plastic molding solutions tailored to your needs.